The gas thermal oil boiler is mainly composed of a burner, a furnace, a circulating oil pump, an expansion oil tank, a chimney and a control system. The thermal oil boiler manufacturing uses natural gas or liquefied petroleum gas as fuel. An open flame is sprayed in the furnace to heat the heat transfer oil, and the circulating oil pump drives the hot oil to circulate between the heat transfer oil boiler and the heating equipment to achieve the effect of heating and temperature control. The boiler is widely used in petroleum, chemical, pharmaceutical, textile printing and dyeing, light industry, building materials, food, road building asphalt heating and other industrial fields that require high temperatures.
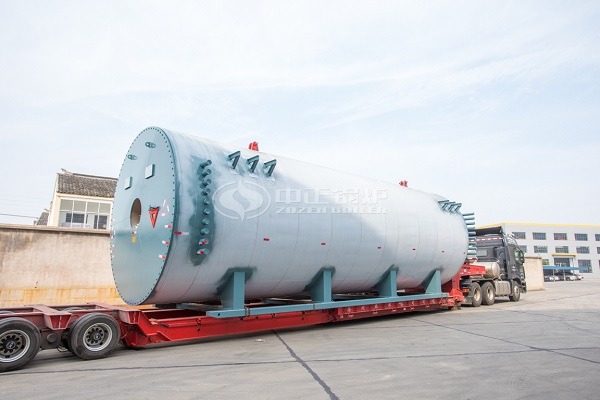
The gas-fired thermal oil boiler has a very compact structure on the heating surface of the boiler body. Because the heating surface of the thermal oil boiler is composed of disks closely arranged inside and outside, the inner coil is a radiant heating surface, and the outer coil forms a convective heating surface with the outer surface of the inner coil. Today, the editor will take you to understand the manufacturing process of gas-fired heat-conducting oil boiler coils.
The thermal oil boiler coil is the most important component of the heat-conducting oil boiler and the only pressure-bearing part. The outer wall of the thermal oil boiler manufacturing tube absorbs the chemical heat generated by the combustion of the fuel. The heat is transferred to the heat transfer oil in the tube through the inner wall of the tube. Whether the thermal oil boiler can be used safely depends largely on the quality of the coil, which shows that the manufacturing process of the coil is particularly important. The thermal oil boiler coil adopts high-quality brand special seamless steel pipe (GB3087) as the raw material of the boiler heat exchange coil. Each steel pipe is 12 meters long, and its strength and ductility are in line with the characteristics of the thermal oil boiler coil. .
The manufacturing process of the gas fired thermal oil boiler coil pipe uses the original pipe butt joint, adopts the angle cutting and grooving machine, makes the welding groove of 30 °, the rust removal before welding and the welding surface is neat, and the penetration rate is strong. The welding machine uses a well-known welding machine brand and uses 360° automatic argon arc welding to ensure welding quality. The coiled tube is bent and formed, and multiple tubes enter the tube coiling mold at the same time. The automatic high-horsepower tube coiling machine is adopted. The multi-branch tube is coiled at the same time.
According to the boiler inspection regulations, the thickness of the parts and materials shall be reduced after bending and processing, and the thickness shall not exceed 0.25mm. For the current welding seams used by our factory, the thickness measurement is performed after processing and bending, and the thickness of 0.15mm is all normal. According to the boiler inspection regulations, 10% X-ray inspection is performed on the welds, and the mechanical properties of the weld samples are tested. The thermal oil boiler is used, in order to adapt to the temperature change and the thermal expansion and contraction of the material, the coil fixing method can be fixed with carbon steel and stainless steel backing to ensure that the boiler is not deformed and prolongs its service life.
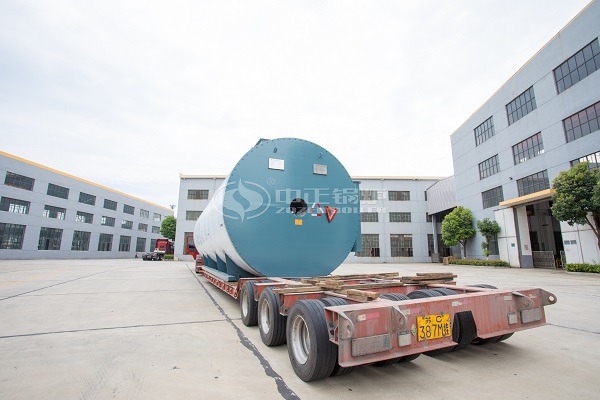
The thermal oil boiler manufacturing with large heating area, high thermal efficiency, high temperature rise and fast hot water supply guarantee. YYQW series boilers are safe and reliable in operation, with low noise, no pollution, high efficiency and energy saving, and easy installation and operation. This series of boiler fuel burns and releases heat in a combustion chamber composed of inner coils. After the radiant heating surface absorbs most of the heat, the high-temperature flue gas enters the convective heating surface for heat exchange.