In the flue gas of diesel steam boilers, some harmful components such as CO2, NOX, SO2 are dissolved in the condensed water, which effectively reduces the emission of air pollutants. At the same time, the large-scale furnace structure and flue gas recirculation technology are adopted, and ultra-low nitrogen emissions can be completely achieved for gas-fired boilers. The NOX emission of the 10 ton/hr steam boiler is ≤30mg/Nm3, which fully meets the increasingly strict national environmental protection requirements.
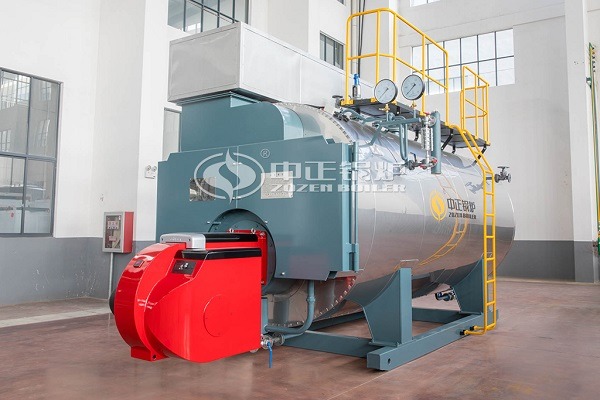
Diesel boilers focus on key technical factors such as the relationship between the condensation rate of water vapor in the flue gas and the exhaust gas temperature, the relationship between the condensation rate and thermal efficiency, and the corrosion rate of condensed water to different steel grades. This series of steam boilers reduce the exhaust gas temperature by rationally designing the heating surface. Ensure that the water vapor in the flue gas reaches the condensation rate required by the design, so that the thermal efficiency of the boiler is greatly improved.
This series of steam boilers adopts a mature three-pass full wet back structure, and the design and maintenance of the smoke box in front of the large opening are extremely convenient. The 10 ton/hr steam boiler adopts low-nitrogen combustion large furnace full mixed combustion and is equipped with heat transfer threaded flue pipe technology. Infused with the principle of flue gas external circulation (FGR) or full premixed surface combustion technology, it has been tested to fully meet the 30mg low nitrogen NOx combustion emission standard, and fully meet the urban heating demand of 30mg low nitrogen emission requirements.
WNS series steam boilers are designed with a large hearth and a full-wave furnace, matched with a reasonable low-nitrogen burner flame. Fully reduce the combustion temperature in the high temperature zone of the furnace flame, effectively control the increase of NOx concentration, and completely meet the requirements of low nitrogen emission. This type of diesel boiler adopts screw heat transfer calculation, screw disturbance design principle, and is simulated by 3D animation. The threaded smoke pipe with small heat transfer resistance is designed, and high-quality seamless steel pipe is used to make it have good heat transfer, low friction resistance and prolong service life.
Diesel steam boilers can be equipped with invisible FGR flue gas external circulation configuration, which can meet the emission standard of 30mg low nitrogen burner. The boiler is equipped with a Siemens solenoid valve, which controls the recirculation rate of the flue gas flow according to the combustion conditions of the burner itself, so as to achieve the ideal low nitrogen emission below 30mg. This series of boiler products is equipped with a built-in condenser at the tail, and all parts are laser-cut and cold-worked. The sealing plate is made of ND steel, and the spiral fin tube with low temperature corrosion resistance is selected. Increase the heat transfer area in a limited space, fully absorb the tail flue gas, reduce the exhaust gas temperature, and improve the thermal efficiency of the boiler. And its structure is a built-in type, which does not occupy the space area of the boiler room at all, and has a wide range of applications.
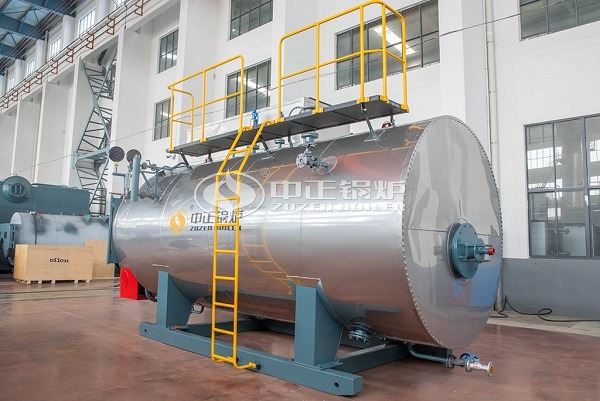
The design concept of the front smoke box of the 10 ton/hr steam boiler adopts a double-layer double-set built-in labyrinth thermal insulation layer and a two-layer structure of heat-resistant layer. The boiler has good thermal insulation performance, and the smoke box panel and smoke box cover are made of integral Q245R boiler steel plates. The blanking of the steel plate adopts the laser numerical control cutting technology, which has small deformation, high assembly precision and good welding forming. The main opening is convenient and the sealing is tight, which is convenient for users to repair and maintain.