Oil-fired steam boilers are widely used in hospitals, schools, textile factories, clothing factories, large supermarkets, garment factories, printing and dyeing factories, hotels, canteens, restaurants, food factories, beverage factories, soy products factories, meat products factories, canning factories, Places of enterprises and institutions such as wineries, pharmaceutical factories, packaging factories, building materials factories, paint factories, swimming pools, etc. The oil-fired boiler body adopts wet-back three-pass, full-corrugated furnace, and threaded smoke tube structure, which has good thermal flexibility. The 2.8MW oil fired boiler tube plate and cylinder adopt a plate edge connection structure. The main welding seam of the main body is a butt joint structure, all of which are welded by submerged arc automatic welding. The overall design is scientific and the structure is reasonable.
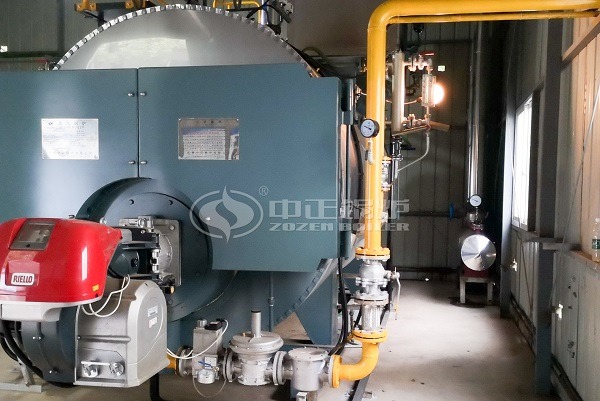
Our company has an internationally advanced large-scale joint-span steel structure production plant with good lighting and reasonable layout. The supporting production equipment is sophisticated, well-equipped, with more than 1,100 sets of various equipment, and multiple sets of various flaw detection equipment such as 400KVA. Product production adopts advanced numerical control cutting, milling, automatic submerged arc welding, argon arc welding, smoke tube tube sheet welding and other new technologies and new processes to ensure product quality. This series of steam boilers adopt a combined control method of mechatronics control equipment and programmable logic controller (PLC). The advanced programmable logic controller (PLC) is used as the “central processing unit” of the control system. The control system is operated through the touch screen, which greatly improves the degree of automatic control and operation reliability of the boiler, and the operation is more simple and intuitive.
The 2.8MW oil fired boiler uses scientific product design, advanced processing technology, and strict quality control. All boiler equipment produced by our factory has a continuous operating life of more than 10 years. The radiant heating surface of the boiler is a fully corrugated furnace, and the convection heating surface adopts threaded smoke pipes. The heating surface is large. The boiler has sufficient heat output and thermal efficiency can reach 92% or more, which is higher than the national regulations.
The fuel of the WNS series steam boiler burns in the furnace with slight positive pressure, the combustion is complete, and the flue gas pollutants are less. The boiler’s flue gas blackness, soot blackness, concentration, noise and other technical indicators are better than the national first-class regional standards. This series of boiler products adopt a specific high-performance computer control cabinet. The boiler can be controlled as a whole through the virtual buttons on the LCD screen of the computer control cabinet. Such as one-key start, temperature setting, pressure setting, etc., the operation is very simple.
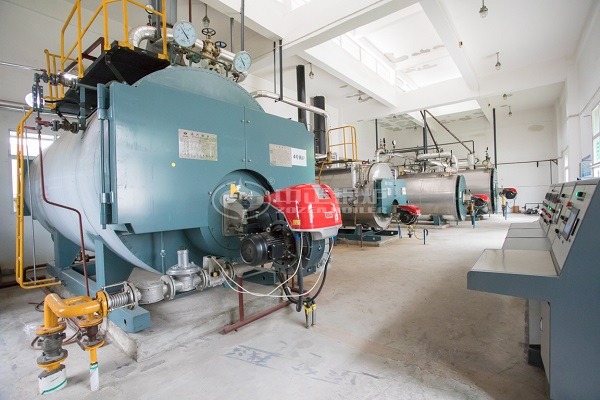
The flame of the 2.8MW oil fired boiler burns with slight positive pressure in the large combustion chamber and is fully extended. This type of boiler has low combustion heat load and high combustion heat efficiency, which effectively reduces the exhaust gas temperature, saves energy and reduces consumption, and is economical in use. The steam boiler adopts an imported burner with a flameout protection device. The function is to detect the combustion situation. When the ignition fails or the combustion is extinguished in the middle, the burner immediately closes the oil (gas) solenoid valve. At this time, the blower continues to operate to purge the residual in the furnace After the combustible gas is purged for 20-30 seconds, the power supply of the blower and various auxiliary machines will be automatically cut off, and the boiler will stop running.