Case Name: Kenya Food Factory 12ton DZL Biomass steam Boiler project
Project Company Profile: the most professional starch sugar manufacturer and application provider
Project type: Complete set project (equipment and supporting equipment provision, installation and commissioning)
Project Location: Kenya
Supporting boiler of the project: 1 set DZL12-1.25-M
Project boiler medium: steam
Project output: 12 tons/hour
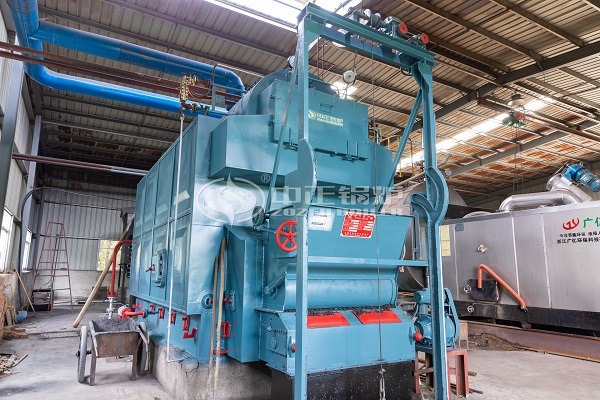
Case Introduction
In recent years, as a new sweetener, starch sugar is being used more and more widely in the food industry, and the starch sugar industry has also developed rapidly in terms of scale, output and variety. Our food factory has been continuously developed in Kenya, and the starch sugar production process requires a lot of steam. For the expansion of production this time, we cooperate with other companies, and their company provides steam for production needs. They ordered a 12 tons/hour DZL biomass steam boiler from ZOZEN’S Company according to the requirements of our food factory for steam quality, using clean energy as fuel and reasonable speed to make the fuel fully fueled, providing high-quality steam and zero carbon dioxide emissions.
Customer Feedback
Due to the gradual expansion of production in food factories in recent years, the demand for steam is also gradually increasing, and the requirements for steam quality are also relatively strict. The steam boiler steam provided by Zozen Boilers this time is sufficient and efficient to meet our various steam production needs.
Boiler Introduction
DZL biomass steam boiler high feeding, pulling to the feeding device. Adapt to the biomass pressure molding fuel, prevent the fire before burning, burning. The inertia separation of smoke and dust at the outlet of biomass fired steam boiler can effectively reduce the dust concentration and the wear of the rear heating surface. Compact structure, smaller installation volume than other boiler with the same capacity, shorten the installation cycle and reduce the cost of boiler room.
DZL series boiler water volume is large, conducive to power failure protection, adapt to load change ability. This series of boiler tube seat flanges are welded by robot. The chain grate is manufactured by our factory, and the test run is 72 hours before leaving the factory to ensure that the tightness of the grate is moderate and does not deviate. The boiler adopts arched tube-plate and threaded smoke tube structure to increase heat conduction and completely solve the problem of rear tube-plate cracking. Chain grate layout, front and rear smoke box panel using CNC plasma cutting machine, neat and beautiful.